Purpose-Built QMS vs General-Purpose QMS: What You Can Expect From Each
Just like the tools at your local hardware store, quality management software comes in many shapes and sizes.
Could you get the job done with any of them? Sure. But just like a physical tool, the software you choose for your QMS will affect the quality of the job you do.
In fact, two companies could conceivably have the exact same quality manual, SOPs, and work instructions—and still have two entirely different outcomes documenting their work and demonstrating total lifecycle traceability.
The reason for this is simple: one company uses a general purpose QMS and the other uses a purpose-built QMS. Despite the fact that they’re both quality management systems, there are significant differences between the two that will determine how your team works.
So, let’s take a look at what you can expect from both general purpose and purpose-built quality management software.
What you get with a general-purpose QMS
We call generic quality management software a “general-purpose QMS” because you can use it for practically any industry. From automotive and aerospace to agriculture and additive manufacturing, companies can customize these tools for nearly any space.
The customization option is attractive because it means businesses can shape the software into a tool that works best for their company—creating their own automated processes, workflows, and notifications based on what they think will work best.
But there’s a catch.
For a highly regulated industry like medical device manufacturing, the customization required to get a general-purpose QMS up and running is enormous. Think about it—you’re taking a tool that could potentially be used for aviation or steel manufacturing and molding it into something that works for your company and complies with all the applicable regulations.
That means, for instance, ensuring that all workflows and e-signatures are compliant with 21 CFR Part 11. It also means integrating risk management into your design controls. These are not necessarily simple customizations to make.
And on top of all that, those customizations must be validated.
Anytime you make a change or new customization within that tool, you’re required to validate it, which means you’re on the hook to make sure everything works correctly and is compliant. Depending on the size of the company and the complexity of the QMS, you could be looking at months of customization and validation—at least.
Taken together, this means that your general-purpose QMS is really a design project. You’ve received a blank slate, and now your job is to design it to accommodate your needs. Is that prohibitive for every medical device company? Maybe not. But it’s the equivalent of assembling the tool yourself when you really just need to get to work.
What you get with a purpose-built QMS
In contrast to general-purpose software, a purpose-built QMS is industry-specific. It can’t be customized for a wide variety of industries because it’s been carefully crafted for the needs of a specific type of company.
But that lack of customization isn’t a drawback so much as it’s a purposeful design choice. If you’re in the market for quality management software, a purpose-built QMS offers an “out-of-the-box” experience. For example, Greenlight Guru’s quality management software is Part 11 compliant on day one, and risk management and design controls are linked inside the workspace to promote a risk-based approach to quality management.
The other big advantage of a purpose-built QMS is that it can be validated by the vendor ahead of time. This may restrict options for customization, but in a highly regulated industry like medtech, pre-validation wipes a huge time commitment off your calendar. In fact, in our 2022 State of the Medical Device Industry benchmark survey, 27% of companies said that their biggest obstacle to quality management was the cost or effort of validating new tools and processes.
Finally, when you use a purpose-built QMS, you can expect a different level of attention to detail. The tool you’re using was probably built by folks in your industry, trying to solve problems that are specific to your day-to-day experience. So, not only will workflows be built according to your needs, but if there is an issue, you’ll end up speaking to someone who’s been in your shoes before.
How to choose between a purpose-built and general-purpose QMS
If you’re seeing a bias toward a purpose-built QMS so far, you’re not imagining things. I obviously have a preference for the type of tool my company sells. However, I want to look at two common considerations for buying quality management software, and offer some perspective on them.
Let’s start with cost. It’s always one, if not the, big consideration for most businesses. My only advice here is to look beyond the sticker price of each option. Time is money, and you should think about how that dynamic will play out over the long run. Consider:
-
How long will it take you to get this tool up and running?
-
How will you document your design and development activities in the meantime?
-
If you’ll need to use a paper-based system for the next six months while you customize and validate a general-purpose tool, what might that cost you in the long run?
-
How much time will you spend on validating new updates or changes over the life of your QMS?
However, there's one more question you need to ask before making your decision: Will people actually use this?
The cold, hard truth is that employees do not always adopt new technology quickly, despite plenty of coaxing from management. In some industries, slow adoption is just an efficiency problem. But in medical device manufacturing, it can lead to huge setbacks. If the tool you choose doesn’t meet your team’s needs, they’ll work on things elsewhere, i.e., outside of the expensive quality management software you just bought.
Not only is that a waste of money, but it makes it impossible to establish a single source of truth. And it exposes you to 483s and even warning letters when FDA comes knocking for an inspection.
Bottom line: your quality management software should meet the needs of your team. Otherwise, it’s not much better than paper.
FREE DOWNLOAD: Click here to see how legacy QMS tools stack up against best-in-class quality management systems with this PDF comparison chart.
Greenlight Guru offers the only purpose-built QMS for medical devices
You probably know where I’m going with this—for medical device companies, there’s no substitute for purpose-built quality management software. Your QMS exists within a highly regulated industry. And beyond what’s required by the letter of the law, there are many best practices and standards that will make life easier for you if you follow them.
Greenlight Guru’s enterprise QMS software is the answer. Not only do you get the enterprise quality management software you need to remain compliant, you have a vast array of tools at your disposal that have been built specifically to help you focus on quality instead of mere compliance.
If you’re ready to start achieving excellence, then get your free demo of Greenlight Guru today.
Etienne Nichols is the Head of Industry Insights & Education at Greenlight Guru. As a Mechanical Engineer and Medical Device Guru, he specializes in simplifying complex ideas, teaching system integration, and connecting industry leaders. While hosting the Global Medical Device Podcast, Etienne has led over 200...
Related Posts
Greenlight Guru Named Premier QMS Software for NIH RADx Initiative
Best QMS Software: Ultimate Guide to Comparing Quality Management System Solutions
Top 7 QMS Tools for MedTech (Plus 4 Bonus Resources)
Get your free PDF
Legacy vs. Best-in-Class QMS Tools Comparison Chart
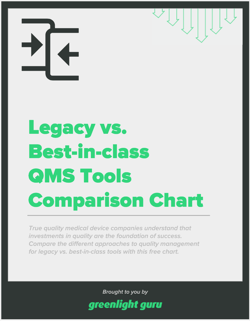