Conducting Quality Investigations in Medical Device Manufacturing
When a quality event, like a product or process nonconformance, occurs in the manufacturing of medical devices, there’s a chance that the safety and efficacy of any affected devices is at risk.
And when that happens, it’s up to the organization to not only fix the issue, but get to the bottom of why it happened in the first place—and ideally prevent it from happening again.
That’s the purpose of a quality investigation in manufacturing. But as with a lot of activities in medical device manufacturing, the execution of a quality investigation can be more complicated than it sounds.
So, if you’ve yet to work on a quality investigation—or just want a refresher—read on. I’ll take you through some scenarios where you might need to initiate a quality investigation and explain how to carry it out.
What is a quality investigation in medical device manufacturing?
A quality investigation is typically launched when failures occur in the manufacturing process, which can include nonconformances related to products, raw materials, components, or processes. These could be identified by complaints, internal audits, or simply someone on the manufacturing floor reporting a process or product failure.
The purpose of a quality investigation is to evaluate the issue at hand, determine the root cause, and take the appropriate action to fix it. If the investigation finds that this problem is part of a larger, systemic issue, then it may require further investigation and corrective actions via your CAPA process.
But keep in mind, quality investigations don’t always have to be reactive. People often forget that you can launch an investigation into potential problems or an observed inefficiency in the manufacturing process.
In other words, quality investigations can also be launched in the proactive spirit of continuous improvement.
Reactive vs proactive quality investigations
To clarify the difference between reactive and proactive investigations a little more, let me give you two related scenarios.
First, let’s say that someone in the cleanroom has to move a part from a machine to a table where the finished parts are typically placed. And this time, that part is dropped onto the floor. Maybe this is a really rare occurrence, and Quality says it’s no big deal—either the part will be scrapped or fixed or re-processed if necessary.
But you may still want to investigate why that part was dropped in the first place. Maybe it’s time to evaluate the process and start asking questions like:
-
Why is this table so far away from the machine?
-
Is there a reason it can’t be right next to the machine?
-
If so, why are the parts being carried by hand? Is there a reason for that?
-
If not, could we use a cart instead?
…and so on and so forth. That’s a reactive start to a quality investigation.
Now, what if the same part, which is big and unwieldy, has never been dropped before? But, as you’re watching the assemblers carry it to the table, you think, “That’s definitely going to be dropped at some point if we continue doing it this way.”
So, you launch an investigation into the process and why it’s been set up like this. You’ll likely be asking the same questions as the reactive scenario, but, crucially, you’re doing it before there’s a problem with any of the parts.
What is the process for a quality investigation in manufacturing?
To give you a better idea of the process you’ll go through during a quality investigation, I want to use a pretty common scenario: a part arrives from a supplier and the packaging is damaged, which leads to the part failing incoming inspection.
The first step, before anything else happens, is to quarantine that part.
That means it’s literally locked up in a cage somewhere that only a handful of people have access to. This is simply to make sure that no one uses the nonconforming part before you have a chance to investigate and determine the disposition. At this point, the Quality department is notified, as well.
Now, technically the next step is to present the nonconformance to your Material Review Board (MRB).
But in reality, after quarantine, you as an engineer are going to be doing a little pre-investigation, let’s call it. What I mean is, you’ll begin looking at the issue, asking people why it may have happened, and generally getting a better understanding of what’s going on before you present this to the MRB.
Presenting to the Material Review Board (MRB)
A Material Review Board is a group of people within a manufacturer’s business that determine what to do with nonconforming products.
The MRB will probably be made up of folks from Quality, Product Development, and Manufacturing. After the nonconforming part is presented to them, they’re in charge of deciding what actions need to be taken, otherwise known as the product disposition. That could include:
-
Reworking the part
-
Using it as is
-
Scrapping it entirely
It could also mean taking action like a 100% inspection of this batch of parts from this supplier, meaning every unit will be inspected, rather than a statistically justified sample.
Additionally, the MRB might decide they need more information about this issue, especially if it indicates a systemic problem. And at that point you may need to open a CAPA. In this example, since it’s an investigation into a supplier, that would mean issuing a Supplier Corrective Action Request (SCAR).
Communication and reporting in quality investigations
Part of the reason you need to have excellent communication and documentation during a quality investigation is to make sure you’re staying compliant with regulations.
For instance, you’ll need to create a change order that describes the disposition of the product, notifies all stakeholders about the change, and gets approved by the appropriate personnel within your organization (probably some, if not all of the people on the MRB).
That change order will describe what needs to happen to this product. So, if you’ve chosen to perform a 100% inspection on the newest batch of parts from this supplier, the change order will describe the activities that will go on during that inspection.
This documentation is crucial, not only for everyone to understand what’s happening, but also because this will all be going in your Device History Record (DHR).
If at any point in the future there’s a problem with one of these devices and the DHR is pulled up, it must have a record of everything that went into the production of this device—including this change order related to parts arriving in damaged packaging.
I know this level of traceability can become problematic for MedTech companies as documentation expands, but that doesn’t have to be the case.
Greenlight Guru’s Design Control Software comes with an auto-generating, auto-updating DHF that helps keep you compliant with both 21 CFR Part 820.30 and ISO 13485:2016. Which means change orders can link to risk items for future evaluation of the design itself.
You’ll be able to create design control objects, link complex configurations, and attach related documents with a single click—all while maintaining full traceability throughout the entire device lifecycle.
But compliance isn’t (and shouldn’t be) your only concern when it comes to communication and reporting.
Going beyond compliance
Something I want to stress is that communication and documentation are about more than just meeting regulatory requirements.
A report about damaged packaging can also be valuable from a business strategy standpoint. If investigations are frequently identifying issues with a particular supplier's parts, that’s something management needs to know about. They may decide it’s time to stop wasting resources on mitigation and find an alternative supplier.
But we’re also talking about the safety and efficacy of these devices. Yes, performing and documenting these investigations properly puts you on the right side of the regulations. But it’s possible to be in compliance and still produce a device that is not as safe or effective as it could be.
Quality investigations should be undertaken in the spirit of ensuring the very highest-quality devices are being manufactured in your facility.
Automate quality processes with a purpose-built eQMS
With the number of steps and sign-offs required in a quality investigation, it’s easy to let them linger or get bogged down in documentation and chasing signatures. Which is why when it comes to quality events, the QMS solution you choose can make or break the quality and speed of your response.
As the leading cloud-based platform purpose-built for MedTech companies, Greenlight Guru’s end-to-end eQMS solution empowers you to eliminate inefficiencies associated with quality event processes by removing excess documentation and automating your quality event processes.
With custom workflow templates, you can incorporate specific, detailed steps and follow your company's protocol to automate quality event processes and always stay on top of issues when they do occur.
Ready to learn more? Get your free, personalized demo of Greenlight Guru today!
Etienne Nichols is the Head of Industry Insights & Education at Greenlight Guru. As a Mechanical Engineer and Medical Device Guru, he specializes in simplifying complex ideas, teaching system integration, and connecting industry leaders. While hosting the Global Medical Device Podcast, Etienne has led over 200...
Related Posts
3 Key Steps for Supplier Risk Assessment in MedTech
Carrying out a supplier audit: when and how to audit your suppliers
Downstream Effects of Inadequate Complaint Handling
Get your free template package for
Nonconformances + CAPAs + Complaints
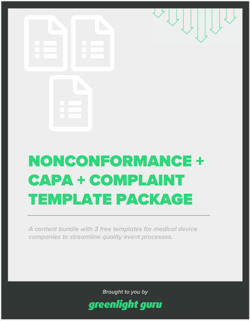