Design inputs are the king of medical device product development.
If a product that is in the market has issues, odds are the issue can be traced back to the design inputs defined during product development.
Design inputs are the foundation of a medical device, and your device is only as effective as the inputs used to create it. Well established design inputs can make the rest of medical device product development easier as a result.
Once you’ve defined design inputs, you are ready to engage in core development. In my opinion, this is one of the most enjoyable aspects of medical device product development.
Core development is the stage in which you’ll be creating your device prototypes and bench testing them. This process leads to establishing design outputs, which define the medical device components and how it will be assembled.
Upon defining design inputs and design outputs, this is the part where your medical device will really start to come to life.
Design Inputs - The Terminology
First, let me spend a few minutes on providing some background on design inputs.
Here is the official FDA regulation for design controls pertaining to design inputs, as found in Part 820.30(c):
Each manufacturer shall establish and maintain procedures to ensure that design requirements relating to a device are appropriate and address the intended use of the device, including the needs of the user and patient. The procedures shall include a mechanism for addressing incomplete, ambiguous, or conflicting requirements. The design input requirements shall be documented and shall be reviewed and approved by a designated individual(s). The approval, including the date and signature of the individual(s) approving the requirements, shall be documented.
ISO 13485:2016 also covers this topic in section 7.3.3 Design and Development Inputs:
Inputs relating to product requirements shall be determined and records maintained. These inputs shall include:
a) functional, performance, and safety requirements, according to the intended use,
b) applicable statutory and regulatory requirements,
c) where applicable, information derived from previous similar designs,
d) other requirements essential for design and development, and
e) output(s) of risk management
These inputs shall be reviewed and approved.
Requirements shall be complete, unambiguous, and not in conflict with each other.
Just by reading what FDA and ISO have to say about design inputs, you can see there are several terms used interchangeably when referring to design inputs:
- Design inputs
- Design requirements
- Design input requirements
- Design and development requirements
- Product requirements
There are plenty more terms used within the medical device industry to describe design inputs. It's important to realize this. I've been in heated discussions with colleagues only to find out after the fact we were saying the same thing.
Design Inputs - Building the Foundation
Medical device product development should be a holistic process that builds upon itself as the project progresses.
Sometimes we are in a rush to get the product to market, but this isn’t a recommended best practice in medical device development. There are times in a project where it really benefits your project to spend a little extra time, and defining design inputs is definitely one of these times. In device development, establishing design inputs can easily take up to 30% of the entire project timeline.
Think about that for a moment. In a 12-month project, defining design inputs can take over 3 months.
The Art of writing Design Inputs
Writing good design inputs is, in my opinion, very much an art form.
Like all art forms, writing design inputs takes practice and dedication.
Your goals when defining design inputs include:
- Capturing all functional, performance, safety, and regulatory requirements.
- Build upon user needs and intended use.
- Make sure design inputs are clear and objective.
- State design inputs in a way that allow you to prove / disprove them.
You have to consider all types of sources and resources for design inputs. Leave no stone unturned. Your design inputs need to be comprehensive, covering all aspects of your medical device.
Where do Design Inputs Come From?
Design inputs should not just be the responsibility of one person. It's a team effort. When a team is involved, you get the benefit of everyone's opinions and experience.
You also should consider all sorts of other sources to help you define design inputs:
- Industry standards
- Regulations
- Previous projects / products
- Competitor products
- End-users
- Prototypes
This is not a complete list, but it gives an idea of what’s involved.
It’s important to remember that user needs should be established first in order to inform design inputs.
Later on, you are going to have to prove your design inputs have been met during design verification.
You should always consider design verification when establishing design inputs. This means you should document your design inputs in such a way that allows you the ability to objectively prove they have been met.
Explaining Design Outputs
Design outputs are often misunderstood, and this can make the process of outlining them a bit tricky. Let me try to clarify this a bit by sharing what FDA 21 CFR Part 820.30(d) and ISO 13485:2016 7.3.4 state about Design Outputs.
FDA 21 CFR Part 820.30(d) states:
Each manufacturer shall establish and maintain procedures for defining and documenting design output in terms that allow an adequate evaluation of conformance to design input requirements. Design output procedures shall contain or make reference to acceptance criteria and shall ensure that those design outputs that are essential for the proper functioning of the device are identified. Design output shall be documented, reviewed, and approved before release. The approval, including the date and signature of the individual(s) approving the output, shall be documented.
Here is the ISO 13485:2016 7.3.4 guidance on design and development outputs:
Design and development outputs shall:
a) meet the input requirements for design and development,
b) provide appropriate information for purchasing, production, and for service provision
c) contain or reference product acceptance criteria, and
d) specify the characteristics of the product that are essential for its safe and proper use.
Records of the design and development outputs shall be maintained (see 4.2.5).
NOTE: Records of design and development outputs can include specifications, manufacturing procedures, engineering drawings, and engineering or research logbooks.
What Is a Design Output?
A design output is a drawing or specification or manufacturing instruction. Design outputs describe all the components, parts, and pieces that go into your medical device. Design outputs describe all assemblies and subassemblies of your product.
Think of it like this. If you were tasked with assembling a medical device from scratch, what documentation would you need to do so? All this documentation that you would need--design outputs.
Design outputs established during product development become the basis of the device master record (DMR) when in production.
DEVICE MASTER RECORD AND DESIGN OUTPUTS
Your DMR is essentially the “recipe” for your device. It contains all the ingredients that you or a third-party would need to manufacture and test the device. Sometimes, there is confusion between outputs and the DMR, but this is easily cleared up. Not all design outputs will be included in your DMR.
As per FDA 21 CFR Part 820.181:
Each manufacturer shall maintain device master records (DMR's). Each manufacturer shall ensure that each DMR is prepared and approved in accordance with 820.40.
As such, the DMR is an example of a required Design output. The two are, of course, very closely connected. The information in your DMR will be used to evaluate your device during the design verification stage.
"Adequate Evaluation" of Design Outputs?
Design outputs must contain and/or make reference to "acceptance criteria". Think of acceptance criteria as a tolerance of sorts. In order to adequately evaluate design outputs, design verification is necessary. And this evaluation is comparing design outputs against design inputs.
Tests are NOT design outputs.
Establishing solid, objective design inputs is the key. Good design inputs make it easier to create design outputs.
And by always keeping design verification (how you prove it) in mind during design inputs and design outputs, these important medical device product development tasks become a lot smoother.
FINAL THOUGHTS
Hopefully this guide has shown you the importance of design inputs and design outputs. Taking the time to craft solid design inputs will feed into the performance and success of your entire project. Your design outputs, on the other hand, are crucial for a successful design transfer, and for testing and verifying your device.
Greenlight Guru’s QMS software was specifically designed to allow for clear, traceable documentation of design inputs and design outputs. Our QMS software is also aligned to the best practices in risk management and change management for the medical device industry. You can click here to take a quick tour of our medical device QMS software.
Looking for a design control solution to help you bring safer medical devices to market faster with less risk? Click here to take a quick tour of Greenlight Guru's Medical Device QMS software →
Jon Speer is a medical device expert with over 20 years of industry experience. Jon knows the best medical device companies in the world use quality as an accelerator. That's why he created Greenlight Guru to help companies move beyond compliance to True Quality.
Related Posts
Design Controls are the #1 Most Cited Issue with FDA
The Ultimate Guide To Design Controls For Medical Device Companies
[VIDEO] Integrating Design Controls & Risk Management To Streamline Product Development (Make Phase)
Get your free eBook
Defining Design Inputs and Design Outputs
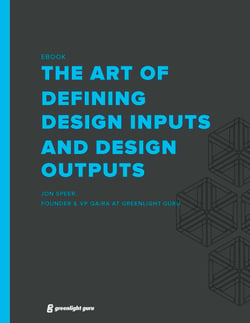