Everything You Need to Know About Root Cause Analysis
At some point, every medical device company will encounter an issue that requires an internal investigation.
Whether it’s due to a nonconformance, complaint, CAPA, or an audit issue, you’ll have to conduct a failure or root cause investigation to pinpoint why the issue occurred in order to resolve it.
For many companies, the news that you need to conduct an investigation may be accompanied by a sense of dread. It’s never pleasant to think about the implications of anything going wrong with a medical device, but don’t let that put you off the heart of the matter.
An investigation can be an excellent learning mechanism—an opportunity for your business to gain valuable insights that spark process and product improvements which only serve you better moving forward.
That being said, investigations can be a source of confusion for many medical device companies, so let’s dive deeper into understanding root cause analysis as a high-level concept, what kinds of steps are involved, and the primary methodologies that are used.
FREE RESOURCE: Click here to download your free copy of our 3-in-1 quality event template package to help you with your CAPA, complaint & nonconformance process workflows.
What is root cause analysis?
Root cause analysis is a method that helps you understand both the primary cause of a problem and why a problem occurred in the first place. Through a variety of approaches, techniques, and methodologies, root cause analysis empowers medical device manufacturers to identify the root cause of an issue, rectify it at the source, and prevent it from happening again.
Root cause analysis is an essential component of corrective and preventive action (CAPA), as well as customer complaints, nonconformances, and audits. In the international standard ISO 13485, the process of identifying root causes and applying necessary controls to prevent similar issues is required for quality management systems, specifically in an organization’s continuous improvement efforts.
As with any QMS procedure, root cause analysis alone does not produce any specific results. Rather, the action taken on behalf of the root cause, as well as the effectiveness of said action, produces the results.
What does a root cause analysis involve?
The steps of a root cause analysis involve procedures to determine what caused the device to break, why it happened, and how you can prevent it from happening again in the future.
Of course, you’ll need to contain and resolve the issue at hand as soon as possible, but the end goal should be to correct the systemic problem and prevent it from recurrence. A successful root cause analysis will almost always involve some variation of these five steps:
-
Create a problem statement. Define the problem taking place by gathering all relevant data and evidence about the current situation. Using the information you collect, your statement should specify the actual impact, potential impact, the focal point of the problem, etc. Keep this statement as concise as possible.
-
Determine the factors that caused the problem. Gather a team of stakeholders directly involved in this process alongside any other experts whose input will be valuable. As a team, brainstorm the possible factors for the problem by uncovering the ‘why’.
-
Identify the root cause. Did deeper by continuing to ask ‘why’ after the first layer of causal factors. Keep at it until finally you have discovered the fundamental cause for the problem at hand.
-
Determine which corrective actions must be taken to eliminate the problem and prevent it from recurring in the future. Make sure that you clearly communicate these corrective actions to the people who will be involved.
-
Review and evaluate the impact of the corrective actions. Determine if the actions can be declared “effective.” If not, make improvements as necessary.
As with any form of a risk-based approach that is taken within a quality management system, documentation is a key component for a successful root cause analysis. Not only does documentation provide traceability for future internal investigations or external audits, it also ensures that any relevant controls are followed to the letter.
In the case of root cause analysis, documentation generally takes the form of established methodologies, tools, and templates.
Types of root cause analysis methods
There are several methods for identifying the real root cause of an issue and coming up with the corrective actions needed to prevent it from happening again.
Here are a few of the most common methods to consider when conducting your own analysis:
‘5 Whys’ Root Cause Analysis
As the name suggests, in the 5 Whys analysis the question ‘Why?’ is asked five times in the course of finding the root cause of a problem.
To carry out a ‘5 Whys’ root cause analysis, you need to gather a team of people who are affected by the problem.
Once you have asked ‘why’ five times and figured out the root cause, come up with an improvement measure you need to apply. Assign the corrective and preventive actions that need to be taken to the members of the team you assembled.
'5 Whys' Root Cause Analysis
Cause And Effect Analysis (Fishbone/Ishikawa Diagram)
Once you have identified the problem, you can use the cause and effect analysis to explore the causes of a problem and its effects. An example of this would be a Fishbone Diagram.
Just as it helps explore the factors that are preventing an outcome, it can also be used to identify the factors needed to generate the desired outcome.
Cause and Effect Analysis
Fault Tree Analysis
Fault tree analysis is a deductive analysis that visually represents the failure path. You can use the fault tree analysis to determine the possible causes of a problem or an event. The fault tree starts with the event at the top and the possible causes are placed below.
Fault Tree Analysis
Pareto Chart
Pareto chart is a combination of a bar chart and a line graph. The length of the bars represent the frequency or cost of faults, and they are arranged in such a way that highlights the most frequent to least frequent. The chart helps prioritize your issues based on the cumulative effect they have on a system.
The Pareto chart is based on the theory that 80% of the total problems that occur result from 20% of the problem causes, referred to as the 80/20 Rule. This means if you have solutions to your major problems, you can also solve a majority of your other smaller problems.
Pareto Chart
Scatter Diagram
Scatter diagrams, or scatter plot diagrams, can be used to visualize the relationship between two variables. Once you have created a cause and effect diagram and identified potential causes to your problem, you can use the scatter diagram to determine which causes are responsible for the variation.
This is possible because the scatter plot uncovers relationships in data. Due to the ease of manipulation in the independent variable, finding correlation means that there is some pattern between X and Y. However, the scatter plot can never “prove” the cause and effect, as this must be established with the researcher’s scientific process.
While the independent variable is plotted along the horizontal axis, the vertical axis is for the dependent axis.
Scatter Diagram
FMEA
Failure modes and effects analysis (FMEA) is a systematic method for evaluating a process. It can be used with the premise that a failure has already happened for which you’re trying to identify the cause and severity of the failure mode, or it can be used proactively.
This would mean assuming a failure or evaluating a process to determine where it might fail, then taking steps to manage any parts of the process that are identified as prone to failure.
Tips for conducting root cause analysis investigations
There are a few key issues that commonly trip up medical device companies. These are often in the area of the tools used for conducting an investigation. Here are a few tips for getting through your investigation procedures:
-
Don’t get hung up on the tool you use. Many businesses let the tool get in their own way by choosing a method that they are not familiar with, hampering them unnecessarily. Find something you can work with and stick with it!
-
Overuse of FMEA is a common mistake. Usually, FMEA is a very good tool if you’re trying to design your manufacturing process or have a singular event that could lead to a failure. If you try to use it to apply to the use of your product, there tend to just be too many variables. Risk Analysis usually requires a sequence of events to occur to lead to a failure when it comes to product use, whereas FMEA is better suited for singular events.
-
Methods, such as fault tree or fishbone, are better where there are a series of events involved.
-
Start with the simpler tools if root cause analysis is new to you. We recommend fishbone or 5 Whys as good methods to start with!
-
Don’t investigate in isolation. A single person will come up with results directly dependent on their own experience. Bring in cross-functional resources to brainstorm—who else has the knowledge?
FREE RESOURCE: Click here to download your free copy of our 3-in-1 quality event template package to help you with your CAPA, complaint & nonconformance process workflows.
Get to the root cause faster with Greenlight Guru
Part of improving your root cause analysis process is having the right tools in place. Greenlight Guru makes it easy for companies to effectively manage not just their risk-based CAPA processes, but also the connected activities of customer complaints and nonconformance management, all in a connected ecosystem where inputs and outputs tell the true story.
Greenlight Guru's software allows you to take the necessary steps to properly define the root cause and trace CAPAs back to their root cause, even if it’s related to design control. In turn, you’ll be able to ensure your corrective and preventive actions are more effective in the long run by providing a verification workflow for your CAPA.
Looking for a CAPA management workflow solution to help you bring safer medical devices to market faster with less risk? Contact us today for your free personalized demo!
Looking for an all-in-one QMS solution to advance the success of your in-market devices and integrates your post-market activities with product development efforts? Click here to take a quick tour of Greenlight Guru's Medical Device QMS software
Brittney McIver is a Medical Device Guru at Greenlight Guru and a Certified ISO 13485 Lead Auditor who works with customers to utilize their eQMS software to streamline processes and maintain audit-ready, regulatory compliance. She began her journey as a Quality Engineer, responsible for carrying out complaint...
Related Posts
What Role Should Quality Play in Bringing a Medical Device to Market?
Ultimate Guide to Corrective and Preventive Action (CAPA) for Medical Devices
The Difference Between Managing Product & Services Suppliers in MedTech
Get your free templates
Quality Event Template Package for CAPAs, Complaints & Nonconformities
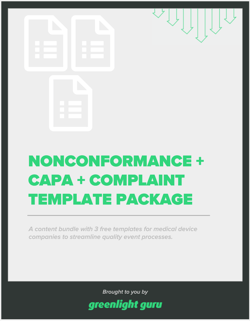