What Role Should Quality Play in Bringing a Medical Device to Market?
Bringing a medical device to market is a tall task for any company, and every department has to work cross-functionally to make it possible.
Even though Engineering, Regulatory, Quality, Production (Manufacturing, Operations, Purchasing, Accounting), Marketing, and Executive Management all have different roles to play, there’s one principle that should link them together, and that’s the pursuit of quality.
I know that quality can be a nebulous term, so today I want to get to the bottom of what quality should mean in a medical device company and the role it should play across departments as you bring your device to market.
Difference between uppercase Quality and lowercase quality
First, let’s talk about what we mean by “quality.” In the medical device industry, the word quality can mean two different things, depending on how it’s used.
On the one hand, you have Quality with a “big Q”. This is how we refer to the Quality department within a medical device company. They’re the ones responsible for implementing a QMS and making sure everything is properly documented for regulatory compliance.
The Quality department is often seen as being solely responsible for what we call “little q” quality. However, when we talk about quality with a lowercase ‘q’, we’re really talking about an ethos—a way of working that gets a better product to market faster, with less risk and a greater impact on patients’ lives.
An overarching goal like that cannot be the sole responsibility of the Quality department. I know it’s cliche, but I have to say it: quality is everyone’s responsibility. Every single person in a medical device company is responsible for ensuring that the devices your company produces are safe and effective and improve the quality of patients’ lives.
What does it look like when you embrace quality across functional areas?
It’s all well and good to say quality is everyone’s responsibility, but what does that mean in practice for the many departments involved in getting a product to market?
If we take a closer look at each department, their specific responsibilities, and how they interact with each other, it should start to make the abstract idea of “quality is everyone’s responsibility” a little more concrete.
Engineering owns the design of the product
Generally speaking, your engineering team will design your product—but that includes a number of different jobs. They’ll need to make sure the requirements for the medical device are defined, and they’ll be hands-on in the building and testing of prototypes.
Engineering is also responsible for documenting design controls during the design and development process. And by their very nature, design controls are quality-based processes. Verifying that design outputs meet design inputs is a quality check - so is validating that the product meets user needs.
Risk management, another design and development task, should be integrated with your design controls from start to finish and will identify safety concerns and help you figure out how to reduce any risks to acceptable levels.
Quality owns the standards of the product
The earlier the “Big Q” Quality is involved in the product development process, the better. There will come a time when you cross the threshold from design and development into production, and that transition process needs to start early.
Remember, your design outputs are your preliminary Device Master Record (DMR). And your DMR describes everything that will be used in production of the device. Quality’s role is to ensure that the DMR is specific and detailed and that quality checks are embedded in the production processes. That all starts during development.
When you get Quality involved early, they can help shape the device’s standards, so that crossing the finish line from development to production is a smooth transition, rather than one department “throwing it over the wall” to another.
Manufacturing owns the consistency of the product
The goal of Manufacturing is to ensure that your device can be produced in a consistent manner over and over and over again. They make sure that the production processes you implement are commensurate with the type of product you’ve developed and the volume you’re producing.
As with Quality, Manufacturing should be involved early on in the design and development process. The prototyping process may even be a good time to start working with Manufacturing and building relationships with them.
When Engineering builds units for verification or animal studies, they have a chance to get Manufacturing’s opinion on best practices and whether or not they’re addressing the right issues.
The earlier Manufacturing understands what you’re trying to build, the more time you have to create an iterative process and avoid any unpleasant surprises about the viability of manufacturing your product later on.
Marketing owns the adoption of the product
Not every company considers Marketing to be a factor in the product development process. In fact, there may be some resistance from the Marketing department itself in participating in that process.
However, Marketing has a big role in the product you’re designing and developing from a quality perspective. There are certain claims you can make, certain things you can say about your product from a regulatory standpoint.
Your messaging, your website, and your literature are usually owned by Marketing, so it’s important they understand the nuances of the device. Involving the Marketing team from the very beginning is the best way to ensure there’s no gap between what the product does and what you say about it as you attempt to speed its adoption.
Regulatory owns the compliance of the product
Focusing on compliance rather than quality is a mistake. That said, there are plenty of regulations your product will need to comply with. The role of Regulatory is to identify the markets you want to pursue, figure out the regulatory pathways in those markets, and make sure the documentation you need for your regulatory submissions is compliant.
If you’re waiting until the point in the process where you need to get regulatory involved for the submission, that’s probably too late. You should welcome them in right from the start because everyone needs to understand the different pathways and options for the device early on.
Executives own the culture of the team
There’s no substitute for a team of individuals who understand and are committed to the mission of quality in your company. There will always be challenges, but a team like that can usually rise to meet them.
It’s true that you can’t establish that culture by executive fiat. However, the Executive team’s job is to ensure that the company is a place where the right type of culture can grow and flourish. Executives have to make sure that Regulatory, Engineering, Quality, Marketing, Manufacturing and anyone else can assert their perspectives on the product and have some healthy conflict.
Steps medical device companies can take toward achieving True Quality
The ultimate goal of bringing a team together around quality is achieving what we at Greenlight Guru like to call True Quality. A culture focused on True Quality is the opposite of a compliance-focused culture. It’s the result of every employee, in every department, making culture their responsibility.
To achieve True Quality, I’d recommend you start by taking three steps:
-
Establish a cross-functional team. You may have noticed a theme in the previous section—every department had a role to play in product development. Yes, engineering has the lion’s share of the responsibilities in designing and developing a medical device, but they are by no means the only ones involved in getting a great product to market quickly. Product development needs to be an enterprise-wide process.
-
Embrace checks and balances that provide an equal say to all functional areas regarding quality. If everyone is truly involved in product development, then you’re going to have some healthy conflict. That’s good. It provides a natural system of checks and balances as people feel comfortable airing their perspectives and having hard conversations about quality.
-
Invest in purpose-built software for the medical device industry to eliminate risk and improve quality. Your time is best spent designing and developing a medical device—not designing the tools you need to do so. When you’re focused on recurring issues with spreadsheets and clunky software, you’re spending less time and energy on quality. With purpose-built software, however, you don’t have to worry about things like building a traceability matrix, for example. Your focus stays on building the most effective, safest medical device possible.
Make sure you have a QMS that enhances your company’s efforts to put quality front and center
Creating a culture of quality is hard work, and it would be a shame to use tools that stifle your efforts at establishing that culture. What you need instead is a set of tools that enhances what you’re doing day-in and day-out.
That’s why Greenlight Guru created our MedTech Lifecycle Excellence Platform. It’s the only software QMS designed by medical device professionals for medical device professionals. Our cloud-based platform helps companies bring safer products to market faster, while reducing risk, lowering costs, and shifting the focus from compliance to True Quality.
If you’re ready for a QMS that matches your team’s commitment to quality, then get your free demo of Greenlight Guru today.
Looking for a design control solution to help you bring safer medical devices to market faster with less risk? Click here to take a quick tour of Greenlight Guru's Medical Device QMS software
Brittney McIver is a Medical Device Guru at Greenlight Guru and a Certified ISO 13485 Lead Auditor who works with customers to utilize their eQMS software to streamline processes and maintain audit-ready, regulatory compliance. She began her journey as a Quality Engineer, responsible for carrying out complaint...
Related Posts
Greenlight Guru and EMERGO by UL Announce Strategic Alliance to Simplify and Automate Global Market Access for Medical Device Companies
Complaint Handling with Medical Device Guru, Brittney McIver
Centese Trades in Paper-based QMS for Greenlight Guru Quality & Achieves 510(k) Clearance
Get your free PDF
Content Toolkit for Quality and Regulatory Teams
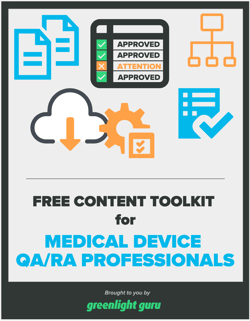