Nonconformance (NC) and CAPA: When Should You Use Each Process?
Your nonconformance (NC) and Corrective Action and Preventive Action (CAPA) processes are two critical elements within your quality management system.
And while the processes share some similar qualities—they are both initiated when there is a problem—they aren’t interchangeable.
Some nonconformances will require a CAPA. Others won’t. Knowing when a nonconformance should trigger a CAPA and what your CAPA process should be used for is essential—yet it’s often a source of confusion for medical device companies.
So, let’s break down the difference between controlling nonconforming product and opening a CAPA, and when each is appropriate.
What is your nonconformance process for?
A nonconformance is a product or process that doesn’t fulfill a specific requirement established by a company, such as a disconnected process or defective product. For example:
-
A manufactured product that doesn’t conform to specifications and is identified during the quality control process is a nonconforming product.
-
A machine that is not placed on the proper setting and produces imperfect materials is a nonconforming process.
You may also experience nonconformances from parts or materials you receive from a supplier. If those materials don’t meet your specifications, they are also nonconforming products.
Investigating a nonconformance can be a lengthy and intensive process, and if not done correctly, can lead to more delays.
Both the FDA’s Quality System Regulation (QSR) and ISO 13485 require medical device manufacturers to have a process in place for controlling nonconforming product. This process should include the following steps:
-
Control the nonconformance
-
Review the nonconformance
-
Determine disposition for nonconformity
-
Perform root cause analysis
-
Take action
-
Monitor for effectiveness
-
Document (this should be done throughout the process)
In many cases, a nonconformance is not part of a larger, systemic issue, and may only require minor actions, such as retraining activities, clarifying work instructions, or refining cosmetic acceptability.
However, if the nonconformance is highly critical to the product, impacts multiple processes, or indicates a systemic issue, then it’s probably time to initiate your CAPA process.
The FDA's guidelines would require an investigation of any nonconformance event and identify actions that would prevent the nonconformance event from recurring.
What is your CAPA process for?
Your CAPA process is the set of procedures by which you take corrective or preventive action once you identify a systemic or highly critical issue in your manufacturing or quality system.
Although nonconformances can be escalated to a CAPA, they are not the only input for CAPAs. Customer complaints, change management, and both internal and external audits can all trigger a CAPA if they turn up systemic issues.
In fact, in 21 CFR Part 820.100, FDA clearly states that manufacturers must have procedures to “identify existing and potential causes of nonconforming product, or other quality problems.”
There are different ways to break it down, but any effective CAPA process should include these five phases:
-
Inquiry and assessment. In this stage, you’ll be creating a CAPA request and submitting it for management review. The CAPA request will be accepted or rejected. If accepted, you’ll move on to the next phase.
-
Pre-investigation. Here, you’ll determine the members of the cross-functional CAPA team overseeing the investigation and finalize your CAPA sources.
-
Investigation. In this phase, you’ll take any immediate actions that are necessary to contain the problem, then begin investigating the issue that triggered the CAPA and perform a root cause analysis (RCA).
-
Planning and execution. In the fifth phase, you’ll develop a plan of action for your CAPA based on the RCA and then execute your plan.
-
Review and verification. The final stage includes steps for approving the actions that have been taken, specifying the steps you’ll take to verify those actions have been effective, and the verification itself.
Although an airtight CAPA process is critical for eliminating systemic issues during manufacturing, our 2022 Industry Benchmark Report found that approximately half of the companies surveyed said their company’s level of competence with CAPA was average or below average. Just 17% said they have achieved “excellence” with CAPA.
What is the relationship between nonconformances (NC) and CAPA?
We know that nonconformances are one of the sources of CAPAs. But it’s important to remember that not every nonconformance will end up triggering a CAPA. In fact, most of your nonconformances probably won’t rise to the level of CAPA.
You should only initiate the CAPA process when a nonconformance is highly critical or systemic in nature. For example, if you notice a recurring problem with a specific component that is used in several of your products; this may indicate a systemic issue, and a CAPA is probably warranted.
Unfortunately, a lot of companies initiate a CAPA for every nonconformance, a term for which we like to call “CAPA happy.” That is, they have an endless number of open CAPAs that suck up all their time and resources.
So remember, you have a nonconformance process for a reason. Don’t be afraid to open a CAPA, by any means, but don’t think it’s your only recourse every time there’s an issue.
Streamline your nonconformance and CAPA processes with Greenlight Guru
Year after year, a poorly defined or implemented CAPA process continues to be the number one reason for FDA issued 483 observations to medical device companies. CAPA and nonconformance processes are crucial to getting a safe and effective medical device to market and keeping it there, but these systems remain a constant source of problems for companies.
At Greenlight Guru, we want to fix that. It’s why we created the only purpose-built QMS solution specifically for medical device companies like yours. It’s also why our solution features a dedicated CAPA Management Software workflow—ready for you to use on day one.
With Greenlight Guru, you can create custom workflow templates and incorporate specific, detailed steps following your company’s protocol to automate your quality processes while ensuring compliance with regulations.
So if you’re ready to change the way you tackle your nonconformance and CAPA processes, then get your free demo of Greenlight Guru's quality management system today.
Etienne Nichols is the Head of Industry Insights & Education at Greenlight Guru. As a Mechanical Engineer and Medical Device Guru, he specializes in simplifying complex ideas, teaching system integration, and connecting industry leaders. While hosting the Global Medical Device Podcast, Etienne has led over 200...
Read More Posts
Dynamic risk management for software-enabled medical devices
Welcome Enzyme to the Greenlight Guru Family
Unpacking Common FDA Compliance Gaps: Pre-Market vs. Post-Market Realities
Get your free resources
3-in-1 Quality Event Template Package
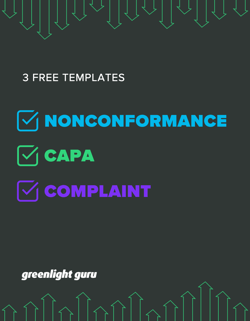