30/60/90 Day Plan to Making an Impact as a New QA/RA Manager
Starting a new job is always a little stressful. But when you’re a new QA/RA Manager, there’s even more pressure than usual. It’s not a stretch to say that the fate of this medical device company is resting on your shoulders.
Okay, maybe it’s a bit of a stretch. But the truth is that designing and developing a great product means nothing if it's not done in compliance with the relevant regulations. And even then, you have to be sure you’re taking the right regulatory pathway to market for that specific device.
While you’re probably ready for that responsibility at this point in your career, having a plan never hurts. So, let me walk you through the stages of your first 90 days on the job and give you some idea of where your focus should be at each part of the journey.
First 30 days as a QA/RA manager - planning and evaluation
The way you handle your first 30 days at your new medical device company will largely depend on one thing: whether or not there’s already a QMS in place. I’m going to tackle each situation for you, but there’s a lot of overlap between building a new QMS and reviewing and tweaking an existing one.
Building a QMS from scratch
It can be exciting to join a medical device company in its earliest stages, but it does mean you’ll be in charge of building its QMS from the ground up.
During your first 30 days, you’ll mostly be getting the lay of the land and getting deeper answers to questions like:
-
What product are we developing?
-
What’s our path to market?
-
What gaps do we need to fill to get there?
The lack of a QMS means you’ll be writing the standard operating procedures (SOPs) from scratch. In this case, my advice is to start with ISO 13485, the international standard for medical device quality management systems.
Take the time to analyze each section and see what applies to your company. Even if you aren’t planning on getting ISO 13485 certified, this is still the best place to start. ISO 13485 is the global standard (even the US is getting on board with their proposed QMSR), and I would highly recommend using it as your guiding light.
Joining a company with an established QMS
At a company with an established QMS, your first 30 days will look a little different. You should still take a deep dive into learning the product and its path to market, but you’ll also need to review the QMS that’s in place.
Basically, you’re still taking the lay of the land, but you’re also assessing whether the previous landscapers made good decisions. This means evaluating every SOP and learning how they affect other roles and departments within the company. If there are issues with any of the SOPs (and there very well may be), you’ll need this knowledge to come up with fixes.
You also need to sit down and evaluate the current regulatory pathway the company expects to take to market. Is this the most efficient and accurate pathway? Hopefully you’re already on the best path, but if not, you’ll need to make those changes as soon as possible.
60 days in: implementation and execution
Your second month at the company will probably involve a lot of iteration. That’s normal. Whether you’re building a QMS from the ground up or streamlining and reorganizing what’s already there, you’ll inevitably rethink some things as you talk with people from other departments and expand your perspective.
Building a QMS from scratch
During this middle period, you’ll be drafting and reviewing SOPs and getting them approved. And if you want to get them approved, you need to know who is approving them and how the SOPs affect certain roles.
I’ve been harping on collaborating cross-functionally, and frankly, I’m not going to stop. You have to understand how your SOPs affect product development, quality, marketing, and anyone else they impact if you want people to actually use them.
This is where you really need to operate with a light touch. Because about 60% of creating these documents involves looking at ISO 13485 and saying, “Okay, this is what we need, so this is what I’m building.”
The other 40% involves talking to the different teams, explaining what you want to do and deliberating with them about whether that’s the best way to go. In other words, there are often items that must be done a certain way and there’s no getting around that; other times, there’s some leeway and it’s up to you to hash it out the best way of doing things with other stakeholders.
At a company with an established QMS
When you already have a QMS to work with, during your second month you’ll be attempting to streamline processes, eliminate inefficiencies, and close any gaps between what you’re currently doing for your QMS and what the relevant regulations require you to do.
Basically, you want to catch any mistakes and build a more robust quality system. Notice, however, I didn’t say “more verbose” quality system. Sometimes people confuse the two, but I can tell you from experience that using more words does not necessarily result in more clarity or a better process. Often, it has the opposite effect.
And you need clarity because the most important factor during this period—whether you have a QMS or you’re building it—will be how well you communicate and educate your colleagues on what you’re doing. When people understand the benefit of following the regulations (or better yet, understand the regulations themselves), they’re much more likely to get behind what you’re doing.
90 days in: verification of effectiveness and adoption
The final third of your first 90 days will be devoted to exploring two questions:
-
Are people actually using what we’ve built?
-
Is what we’ve built effective?
Building a QMS from scratch
Just because you’ve spent two months writing SOPs and building a QMS out of thin air, that doesn’t necessarily mean people are using it. Your job now is to verify that people are actually following the SOPs. And if they aren’t, you need to find out why.
In my experience, a lack of training is often the reason for a lack of adoption. When you were writing your SOPs, you spoke to the people who needed to approve them. You educated them on what needed to be done and you got them on board.
The thing is, there may be people farther down the chain who need to be following these SOPs, but didn’t get the same information from you. They might be sitting there thinking to themselves, “What is the point of this?”
Again, it comes down to your ability to work with people outside your department and educate them on the importance of using the QMS and following the SOPs.
At a company with an established QMS
For a QA/RA manager working with an established QMS, your goal will be more about verifying the effectiveness of any changes you’ve made.
If you’ve rooted out inefficiencies and streamlined processes, you may assume those changes were effective, but you can’t just assume. You need to continue communicating cross-functionally and verifying that the changes you’ve made have resulted in more efficient and effective processes.
What’s next: life after the first 90 days
I’ll finish up with a story. It’s about one of the best quality managers I ever worked with—the VP of Quality at a medical device company I used to work for.
I was new to the organization the first time we met, but he already knew my name. He walked right up to me while I was making some copies and introduced himself in a way I’ll never forget.
“Hey, Etienne, I just wanted to introduce myself. I know you’re a new manufacturing engineer and I’m excited to have you here. I just want to let you know who I am and what the quality engineers do. Our job is to make sure that we follow the regulations and follow the standards. Everybody in this organization is liable if someone gets hurt, but our job is to protect you guys so that never happens."
It’s true that Quality is often viewed as the police of the organization. I used to think like that. But as I matured and spent more time in the industry, I grew to appreciate the work they do.
I think back to the way he made sure I knew who he was, what he was doing, and why - that’s the essence of a great QA/RA manager distilled.
If you’re starting in a new QA/RA role and you’re looking for a QMS solution that will not only complement, but accelerate, the work you’re doing, then get your free demo of Greenlight Guru today.
Our comprehensive, out-of-the-box solution is based on the latest FDA and ISO standards, as well as best practices of medical device manufacturers who lead the industry in production of high-quality devices, and it’s an invaluable tool for medical device professionals looking to deliver the safest, most effective products to patients.
Looking for an all-in-one QMS solution to advance the success of your in-market devices and integrates your quality processes with product development efforts? Click here to take a quick tour of Greenlight Guru's Medical Device QMS software
Etienne Nichols is the Head of Industry Insights & Education at Greenlight Guru. As a Mechanical Engineer and Medical Device Guru, he specializes in simplifying complex ideas, teaching system integration, and connecting industry leaders. While hosting the Global Medical Device Podcast, Etienne has led over 200...
Related Posts
Medical Device Compliance: Regulations, Standards, and Solutions
5 Common Regulatory Pitfalls in the Medical Device Industry (and How to Avoid Them)
3 Key Steps for Supplier Risk Assessment in MedTech
Get your free eBook
Ultimate Guide to ISO 13485 Quality Management System (QMS) for Medical Devices
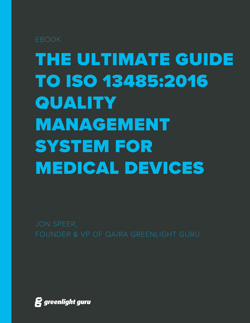