How to Manage Complex Downstream Design Changes to Your Medical Device
It would be nice if every device your company ever produced got to remain on the market for decades, completely unchanged.
That’s not the world most MedTech professionals live in.
Changes to a device that’s already on the market happen all the time. And while there are a multitude of different reasons that a change might be necessary, the steps you’ll take to address any required change will follow a similar path.
If you’re staring down the barrel of a major request like this one, it always helps to start at the beginning and take it one step at a time.
BONUS RESOURCE: Want to streamline your change management process? Click here to download your free copy of this Change Order Template.
Build a cross-functional team
Before we get into the exact steps you’ll need to take to make this change, let’s talk about who you’ll need to work with. Because this isn’t a one-person job. In fact, to make this happen at all, you’ll need to build a strong cross-functional team that will include at least:
-
Product development. This is something of a no-brainer, but a large part of managing this design change will be going back through design controls and examining your design requirements, so you’ll absolutely need product development’s involvement.
-
Quality. A change in materials is not a minor change. Your assumption might be that the product was over-engineered and that a change to a slightly less robust material won’t affect anything. But what if you’ve been getting complaints about failures in the material you’re currently using? Quality needs to be involved because they have information that will affect your decision-making.
-
Regulatory. Changes to your product will have regulatory implications. In the US, depending on the situation, you may need to use a letter to file (LTF) or a special 510(k) submission.
There may be other people you need to loop in and work with—like marketing or sales, for example—depending on your situation. But these are the key players that you absolutely need on your team as you work through this design change.
Start from the beginning: the device’s design controls
It always helps to break a complex project up into its constituent steps. So let’s think about what those are and where you need to start from. In this case, it’s design controls.
Go back to your user needs and design requirements
For this example, let’s say you need to change the material that part of your device is made of.
The decision to use the original material was made in design controls, so you’ll need to go back and look at your initial design requirements. Was there a user need that drove the decision to use this particular material?
For instance, maybe one of your user needs was that this device must be able to support an arm throughout the entirety of a surgery. And that user need drove a requirement for a specific tensile strength. The requirement for that tensile strength is why you chose this material in the first place.
Maybe you can still meet that strength requirement with the new material, but at some point, you have to compare the two materials.
Does this new material affect anything? Does it affect how the user interacts with it? Does it hold up to our strength requirements? And you can’t forget about risk management during this process, either. What are the risks of using this new material?
Let’s say at the end of your analysis of design controls and risk management, you’re able to conclude that you can use the new material with no additional risk. Great! Now you have to verify it.
Time for verification and validation
The analysis of materials and tensile strengths and probabilities and severities is one thing, and it’s important to do all of that carefully. But once the new design (with the new material) is ready, you still have to verify via testing that the design outputs meet the design inputs (such as your requirement for tensile strength).
Not only that, but any design change will require you to validate the device’s design against its user needs, just as you did the first time this device was developed. Once verification and validation have been performed, you can lock the design once more and update the Design History File (DHF) and any other paperwork, just like you did originally.
Review the design transfer
The final step here concerns your design transfer. It may very well be that this change in material necessitates a change in type of machine and or even the contract manufacturer you’re using to produce this part.
The first time around, your CRO performed process validation (IQ, OQ, PQ) on the machine that manufactured the part. But if you’re changing the manufacturer you’re using or the machine that makes this part, the master validation plan will need to be updated. You’ll also need to update the Device Master Record (DMR) because the design outputs have changed.
In a sense, this entire process is really an exercise in traceability. If your design controls were all impeccably documented when the device originally went through D&D, then none of this should be extraordinarily difficult to find and update as you go. If they weren’t well-documented, then… it will certainly serve as a reminder of how important it is to get documentation right the first time.
Every situation is unique
The example I’ve given of a material change is purposely over-simplified for clarity’s sake. But I do want to note here that the reason you’re making this change will dictate some of what’s required.
For instance, if you’ve been getting complaints about this device and have decided to change materials before FDA steps in, then you may need to do a voluntary recall or report adverse events to FDA through MedWatch.
If you’re changing materials in order to streamline the manufacturing or shore up supply chain issues related to your device and increase production as you expand into a new market, for instance, that’s a very different scenario.
So just keep in mind that while the basic steps for going back through design controls will typically be the same, there may be some requirements I haven’t explicitly stated here that will apply to your situation.
When it comes to design changes, don’t blindly carry out orders
Finally, this might be a bit controversial, but I’ll always advocate for MedTech professionals to think independently and consider every aspect of what they’re being asked to do. Just because you’ve been asked to change a material (or any other design change), that doesn’t mean it’s necessarily a good idea.
I like to talk about the three legs of any MedTech business:
-
Ethics (focused on patient safety)
-
Edicts (focused on following the law)
-
Economics (focused on keeping the business open)
A design change may be fine from the standpoint of patient safety. And you may be able to make that change while staying compliant with every regulation.
But does it make economic sense?
For example, you may have to build actual models of the device and perform destructive testing on them in order to verify this design change. You may need to do both accelerated and real-time aging tests.
What if these are extremely expensive devices? All this necessary testing could cost the company half a million dollars just to perform verification on the design change. Does management (or even engineering) understand the true cost of making this switch?
I’d encourage you to take some time and think carefully about what you’re being asked to do before you dive in. It’s possible that the cost of switching is not actually worth the perceived benefit.
BONUS RESOURCE: Want to streamline your change management process? Click here to download your free copy of this Change Order Template.
Greenlight Guru’s powerful eQMS solution helps you manage complex design changes with ease
Downstream design changes are just a part of life in the MedTech industry. And while they can be a little overwhelming at first, the problems that occur when trying to make a design change often occur because of problems with a company’s QMS. Missing documentation, disconnected systems, paper files—it can all turn a simple design change into a massive undertaking.
At Greenlight Guru, we built our eQMS solution to be fully traceable, with an intuitive user experience that makes finding documents—and seeing their connections throughout your QMS—as simple as possible. Greenlight Guru is your team’s single source of truth, no matter how complex your devices’ design controls or risk management become.
So if you’re ready to see how our QMS platform can save your company countless hours spent digging for documents, then get your free demo of Greenlight Guru today!
Etienne Nichols is the Head of Industry Insights & Education at Greenlight Guru. As a Mechanical Engineer and Medical Device Guru, he specializes in simplifying complex ideas, teaching system integration, and connecting industry leaders. While hosting the Global Medical Device Podcast, Etienne has led over 200...
Related Posts
Unlocking U.S. MedTech Market Access: State-Specific Compliance Pitfalls Medical Device Companies Miss
How to Build a Medical Device Business Case in 5 Easy Steps
3 Key Steps for Supplier Risk Assessment in MedTech
Get your free Template
Change Order Template
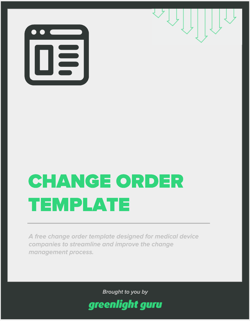