13 Tips For Audit Etiquette Every Medical Device Company Should Know
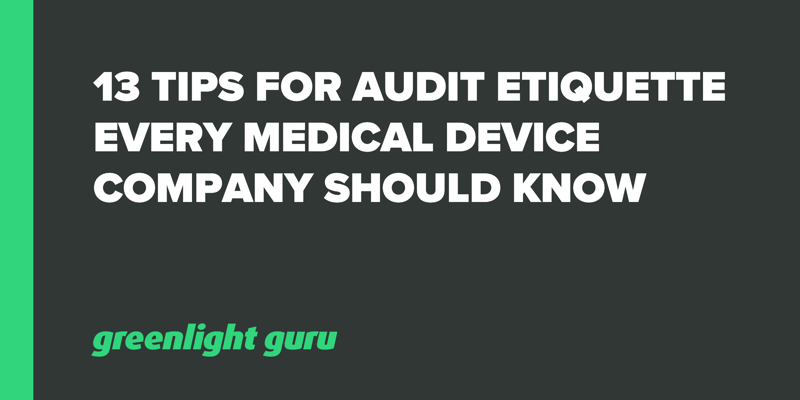
I love audits. Seriously! It is a hybrid experience, like a kindergarten show-and-tell with a classic case of “Whodunit?!” Dare me to trace back a record from three years ago. I’ll gladly accept!
Auditing is a rewarding experience. I invite you to keep an open mind and hear me out as I explain why...
There is nothing like the feeling of handing a packet of documents to an auditor, after working diligently on a process or procedure for MONTHS, and watching them page through the evidence.
Your heart is beating with every turned page. As they near the end of the documentation, you watch the auditor as they pause, return to an earlier page, re-read a section, and return to the end of the procedure or protocol.
They take notes. What are they writing? What do they think I might have missed? What will they want to see next? You sigh a breath of relief as the auditor places your documentation to the side. The silence breaks: “Ok,” they begin. “Let me see your….”
It goes on and on for days at a time: the anticipation, the review with a fine tooth comb, the near constant feeling of walking on eggshells. But what if audits weren’t scary? What if audits were just another day?
As a certified Lead Auditor for ISO 13485 and auditee in countless experiences, I will share with you provenly effective tips and pointers for how to prepare for an audit and how to ensure your audit runs smoothly.
#1. Remind/warn your company the audit is happening.
Ensure the appropriate leadership, SMEs, and support will be onsite. If they are offsite, ensure they can be reached or have assigned back-ups to handle any questions.
Remind the front desk of guest/visitor procedures. Do not allow the auditor to roam the building and office. Have the front desk receptionist notify the auditee so they may escort the auditor to the proper area.
Take the time to remind the company of safety and cleanliness procedures which may be “rusty.” Not only is it a good idea to refresh their memories, but the last thing you need during an audit is a safety incident or mishap.
#2. GEMBA and perform a dry-run prior to the audit.
Developed by the famous automaker Toyota, Gemba Walk is a commonly used Lean and Six Sigma practice for teams to gather information by observing and interacting amongst one another.
Prior to the audit, take a field trip to the floor to observe processes. Even though internal auditing and standard work are likely part of your processes, how would a process look to an outsider? What questions might an auditor have about a process? Physically, how does the observation area look? Try to have the perspective of an outsider and determine how you can put your best foot forward.
#3. Audit your own records.
Sounds obvious, but make sure your records are up to date. Are you late on performing your management review? Are all training records complete? Have you uploaded the most current calibration records? If not, better hop to it.
If you have to point to a systemic issue, do your due diligence now rather than face an uncomfortable discussion later. For instance, if you are late to perform your internal audit, don’t push it under the rug. Open a CAPA to determine a root cause and create an action plan. While the auditor will likely write some sort of nonconformance during the audit, you at least have an action plan to point to instead of saying “I don’t know what happened.”
#4. Prepare and anticipate!
Actually read through the audit agenda you should have prepared.
Assign resources accordingly, especially if you have more than one auditor in more than one room. You might be a quality superhero, but no person can be in the same room at once. Using the agenda, alert your SMEs of where they need to be and when.
Prepare sample records, within reason.
Anticipate the needs of the auditor. If this is a follow-up audit from a previous year, know where to find the corrective actions implemented. If the auditor is looking at preventative maintenance, know where your PM schedule is.
Know how to create a list of your QMS procedures and open CAPAs. This way, you can play it cool when the auditor asks you for the information. Greenlight Guru makes your company audit-ready by allowing users to create unique filters and lists of documents.
#5. Make plans for lunch.
If your auditor is with a federal agency, such as the FDA, they will likely go offsite to eat. If you are hosting the auditor through lunch, order lunch early. No one wants a “hangry” auditor.#6. Establish the audit space.
Ensure the room where the auditor will work has plenty of outlets and table space.
If space permits, set up a war room away from the auditor’s area to prepare and review records prior to passing them onto the auditor.
Ensure your war room employees are well versed in the procedures and processes. Bonus points if they can find the exact section in the procedure where the auditor’s question is answered.
#7. Answer only the question asked.
Do not mistake this for withholding information. Because auditing is evidence based, the auditor will guide you to where they want the conversation go. The classic example is “Do you have X procedure?” The answer is not “Yeah we just revised it and it has been waiting on Quality to approve for the past two weeks. Man, is that team slow! We can’t get anything done. I don’t know how we are supposed to close CAPAs when we can’t even approve procedures!”
First of all, keep your emotions out of the response. You may be frustrated with the speed of review but that has nothing to do with the question and, now, you painted the quality team in a bad light.
Where do you think the auditor is going to go next? They could ask for document review analytics. They could ask for Quality team training. They could ask for an open CAPA list and KPI (key performance indicators) on CAPA close time. All of that when you could have answered “Yes.”
PRO TIP: My goal is to talk as little as possible. Let the documentation and records do the talking.
#8. Relatedly, enjoy the silence.
Seriously. Do not feel the need to make small talk. Once you have answered the question, stop talking! Think about lunch or count backwards from 1000.
While you are waiting for the next question, anticipate where the auditor could go next? Is the auditor reading your environmental controls SOP? Well, chances are they will ask for temperature monitoring records next. Oh, and where are your calibration certificates for your temperature monitors?
#9. Only provide the auditor with what they ask for.
Even if you have the temperature monitoring records and calibration certificates ready, do not hand over the records until the auditor asks for them. Again, let the auditor guide the conversation.#10. Keep it positive.
During the audit is not the time to complain or be negative. Do not argue with the auditor EVER. If you do not agree with something, support your viewpoint with objective evidence. If you do not understand a finding, ask for clarification during the audit rather than bouncing emails back and forth with the auditor after the closing meeting.#11. Answer in absolutes.
You do something, or you do not. If it is yes, no, or in between, there needs to be a process. Don’t say “We sometimes do it this way” or “This person does it one way but I do it another.”
If you don’t know, you don’t know. If you are unable to answer a question, say “I don’t know” and find someone who does. Do not make something up.
#12. Stay with the auditor.
Do not let the auditor wander the operations floor alone. Keep someone from the company with the auditor at all times. This will allow the auditee to answer any questions the auditor has, take notes of items reviewed, and protect the auditor from safety incidents.#13. Keep track of records reviewed and conversations held.
If resources allow, have a scribe be a part of the audit to record all records viewed and comments made. This is invaluable information when you are responding to audit findings or when you are writing a daily summary to management.
In between audit days, do not throw anything out. The auditor may ask to see a record again while they are writing their summary.
|
Ace your next audit
Greenlight Guru's medical device QMS software with Audit Management and Document Management workflows allow your audit team to stay ready, so they do not have to scramble to get ready last minute. By having your procedures and records at your fingertips, preparing for an audit takes an afternoon, not a week.
Save hours (and trees) printing off documents and present the necessary information from your eQMS in real time, to the auditor. Greet your auditor with confidence while knowing you can answer their questions with organized, objective evidence.
Looking for an all-in-one QMS solution to advance the success of your in-market devices and integrates your quality processes with product development efforts? Click here to take a quick tour of Greenlight Guru's Medical Device QMS software →
Taylor Brown is a Medical Device Guru, certified Lead Auditor for ISO 13485, and a card-carrying Quality Nerd. She got her start in the industry as a technical writer and quickly became an audit readiness and support specialist, traveling around the United States to establish ISO 13485 compliant quality systems. She...
Get your free checklist
Free Checklist for QMS Internal Audit
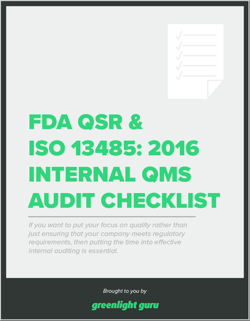